Track production cost discrepancies and keep data correct all the time
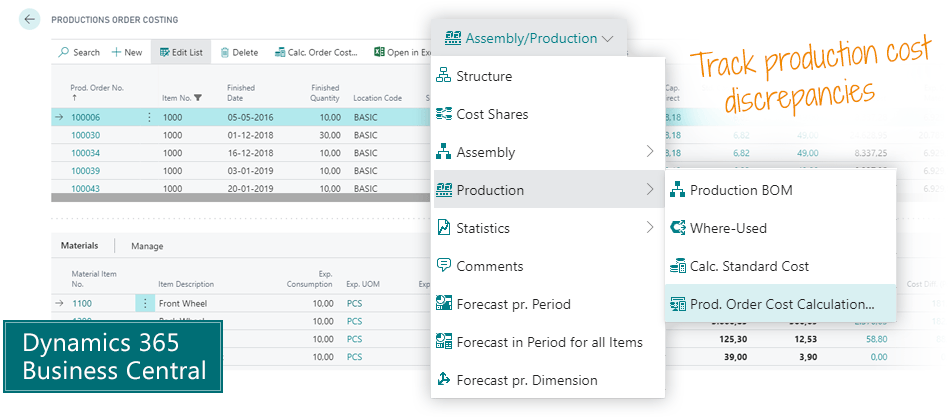
Production Order Cost Calculation is the intelligent way to find discrepancies in productions costs – and correct master data in Microsoft Dynamics 365 Business Central.
Track production cost discrepancies
In standard Business Central you can see what an item’s resource cost is at an individual level or accumulated level.
With Production Order Cost Calculation you can follow it all the way down to the operational level and distinguish between Setup time and Operation time, as well as between direct and indirect costs.
This allows you to quickly compare what the cost should have been according to the Routing and BOM, in relation to what the actual cost was. Thus, you can quickly and effectively correct the master data.
Comparison of master data with records
When a Production Order is finished, you can do a final calculation of the cost.
In doing so, the projected cost of the order is calculated and divided not only into all Materials and all Operations, but it is also broken down into direct and indirect costs.
The projected cost is compared with the actual registered costs and discrepancies are shown both as actual amounts and as percentages.
Discrepancies are shown separately for the total production order, for all materials on the order’s BOM and for all operations on the order’s routing.
Focus on the largest discrepancies
From Production Order Cost Calculation you can open a new window where all the lines can be overviewed.
This enables you to periodically search for the lines with the greatest percentage of discrepancies – or those that have the greatest financial impact – and examine those Routings and Bills of Materials in details. This way, you can quickly find the largest discrepancies.
Assess data over time
The calculated data is stored in a table, and gradually you build a history of production data. You can look back in time and compare data from the same operation and find significant discrepancies.
When you find an order with discrepancies in any operation or material consumption, you can easily compare it with previous orders and find out whether the discrepancy is a one-off or something symptomatic.
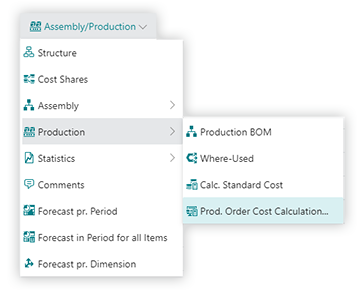
Main Benefits of Production Order Cost Calculation
For Finance:
- Avoid large inventory discrepancies at the annual inventory count – by getting warehouse and items-in-assembly values that match all the time.
- Focus more on discrepancies while also improving quality faster.
- Make sure data is correct and enable the production to deliver accurate projections to the finance department.
For Planning:
- By comparing the projected cost and time with the registered cost and time, you can see the deviation of material consumption and time registered.
- Quickly find the largest and most important discrepancies in operations or materials you want to correct right away.
For Production:
- The organization will get a habit of correcting data continuously.
- This easy tool to track discrepancies will constantly keep data correct.
- Be able to explain the cause of discrepancies much more effectively.
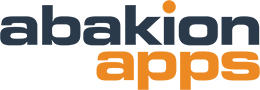
Abakion is your one-stop shop for Apps
Getting started with the app
Download and install now
Read the step-by-step guide
Watch user guide videos
Production Order Cost Calculation pricing
Single app
Single user is DKK 120,00.
The more users you subscribe to, the cheaper each becomes. Watch video about the price model »
As part of the App Bundle
Talk to a real human
Have a chat with our app managers Bo H. Hansen and Thomas Halse about pricing and subscriptions:
appsales@abakion.com
We will reply in English.
Support
If you have specific questions about functionality or how to get started, you may contact our support team at frontdesk@abakion.com or call us at +45 70 23 23 17. We will help you find the right video guides, if available.
We strive to provide you a qualified response as quickly as possible, at least within 24 hours but often much quicker.
At all times we will keep you informed about who is working on your support inquiry and how soon you can expect a response.